The scope of the renovation work consisted of the evaluation of the existing structures, the retrofit of structural deficiencies, and specific upgrades to isolated portions of the buildings to meet the loading requirements for various occupancies ranging from multiple light industrial to artisanal use. The primary hurdle involved devising a systematic approach to appraise the varied structural elements within the complex and assessing the structural soundness for each intended new use.
About the project
221 McKibbin Street
Brooklyn, NY
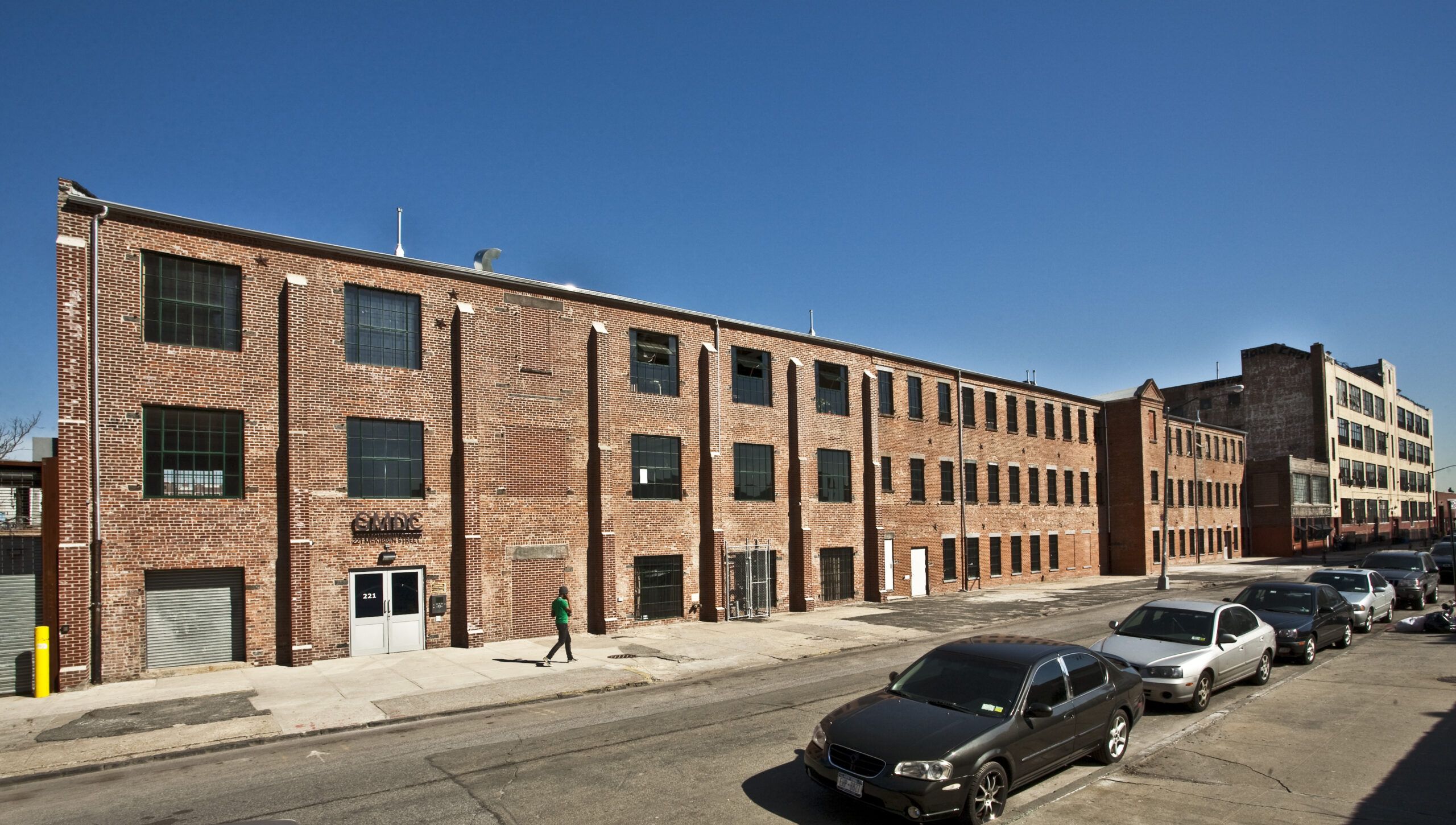
Client
Greenpoint Manufacturing & Design Center
Architect
OCV Architects
Location
Brooklyn, NY
Completion date
2009
The McKibbin Street Industrial Center underwent extensive renovation, revitalizing buildings dating back to the 1850s and 1930s. The newly transformed complex now offers 72,000 square feet of space dedicated to light manufacturing and artisan work. While contemporary infrastructure was integrated, the historic brick facade, interior, and 1930s-era multi-light steel windows were meticulously restored to their original specifications. This property stands as the sole remaining structure of its kind in Brooklyn, originally serving as a rope manufacturer during the borough's prosperous maritime era. Designated on the National Register of Historic Places, it earned the 2009 Historic Preservation Award.
Assessing the Existing Conditions for Adaptive Re-Use
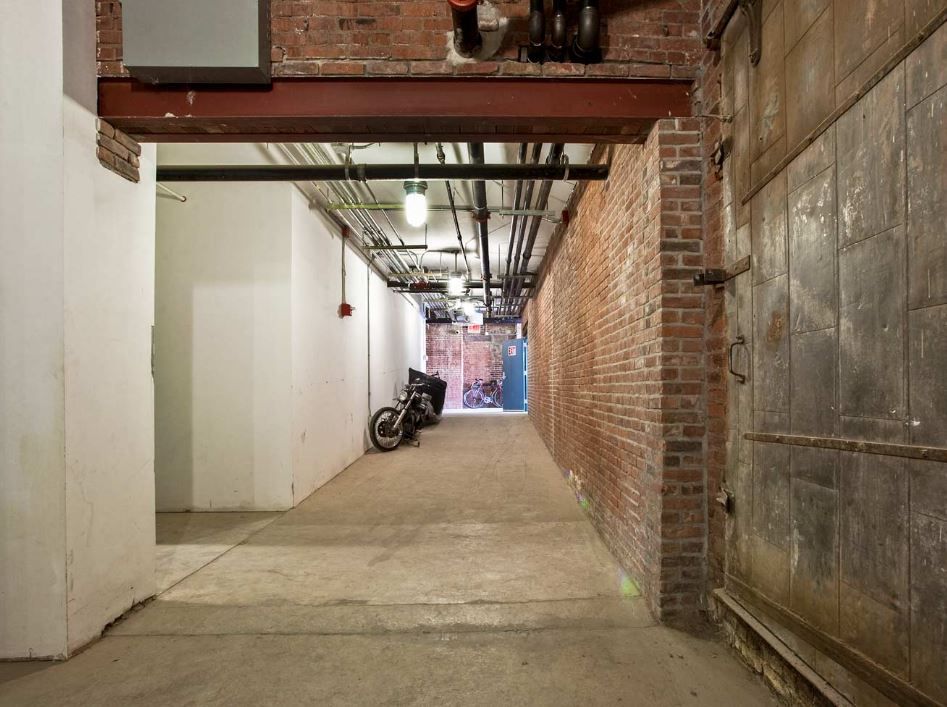
Roofing and Floor System
The existing roof truss is a 41-foot-long timber double-howe type, with all vertical members made of steel rods. Multiple layers of a variety of roofing materials were removed in order to reduce the rood dead load and quantify the loading capacity of the roof. Roof joists with large deformations were replaced by sawn timbers of various sizes, depending on the spans. Similar to the layers of roofing material, layers of flooring needed to be removed in order to properly evaluate the condition and strength of the over 100-year-old timber floors. Removal of the flooring material revealed rotted and fire-damaged areas. Joists and girders that showed signs of severe deterioration and large deformation were replaced by new timber joists and steel beams. Helical piles incorporated with grade beams were designed to strengthen the wall footing at the cracked south-west corner of the building. The advantage of helical piles is mainly its minor disturbance to the existing building during installation. The piles prevent further cracking of the existing wall and increased the building’s integrity.
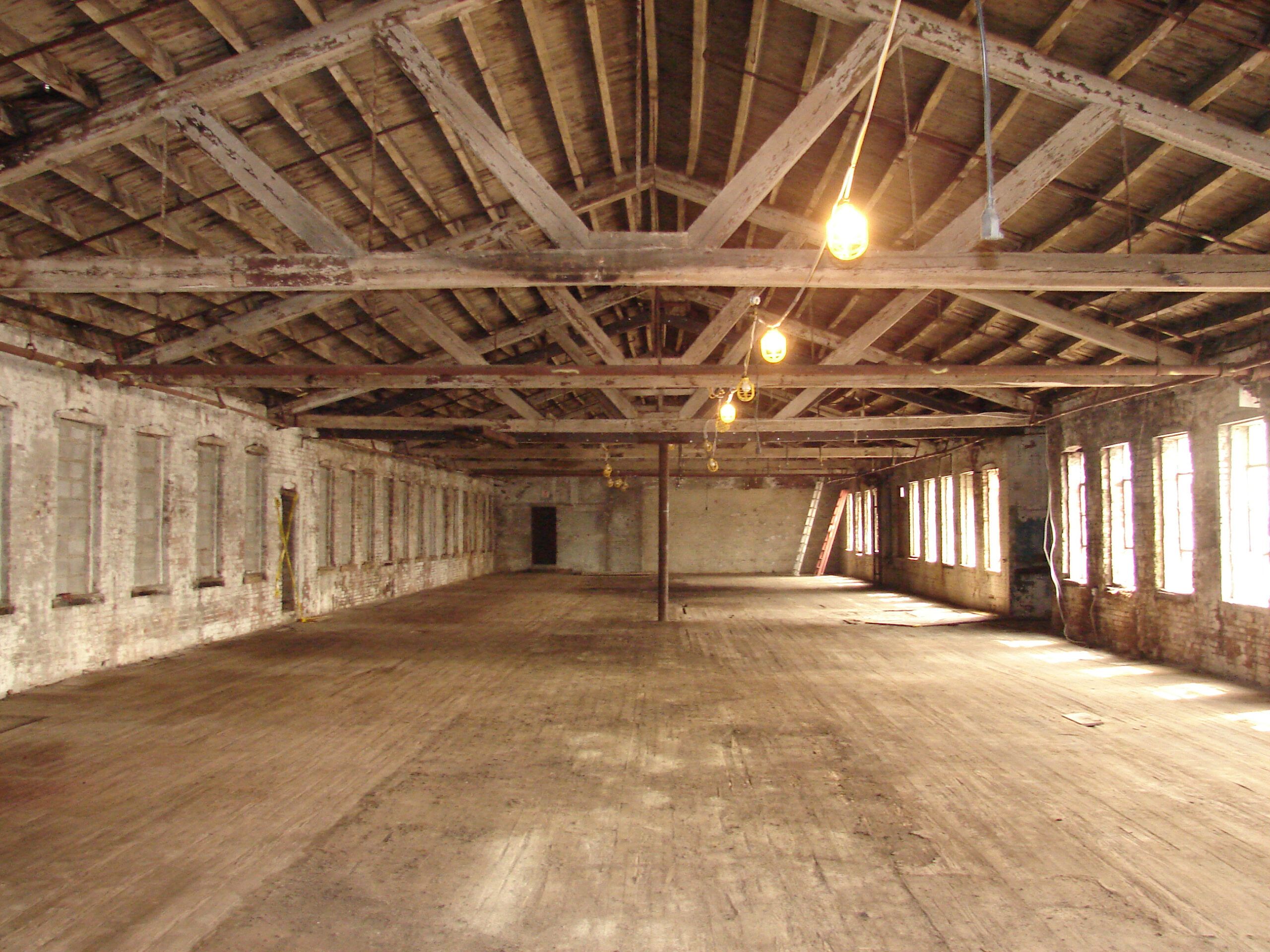
Masonry Walls and Columns
To retain as much of the existing structure as possible, portions of walls with compromised masonry were disassembled. These sections were re-built and tied back to the stable portions of the walls. Columns with severe corrosion and large incline were replaced with new steel columns. Corresponding concrete footings larger than the original ones were designed to accommodate the poor bearing fill.
Services
Trusted Partnerships
Affiliations and Accreditations
Similar Projects
Projects Gallery
Approaching
25 years of
engineering
design solutions
We proudly offer our integrated services to architects, building owners, and developers throughout every project phase. Our solutions not only conquer intricate design hurdles but also enhance ease of construction and maximize energy efficiency, ensuring your project’s success at every level.